ABOUT BOATO PACK
BOATO PACK was founded in the 1950’s. The production at that time mainly consisted of small machines with one or two production lanes. In the 1980’s the company called Boato Tecsystem later became BOATO PACK.
At the beginning of the 1990’s Boato Pack was purchased by the present owner. At the time of this take-over, the technical level of the machines was only an evolution on the basic models that had been produced during the course of the preceding 40 years. The range was limited to produce sachets with only 2 or 3 types of volumetric dosers, having a wide dose range and running at a very slow output speed.
The new management decided to move forward to a new range of machinery able to satisfy the needs of the most important customers – co-packers, Multi-National industries and the like.
OUR TECNOLOGY
More than all the characteristics such as speed, efficiency, low maintenance, etc…, two technological characteristics differentiate our machines from others, flexibility and “turnkey” solutions.
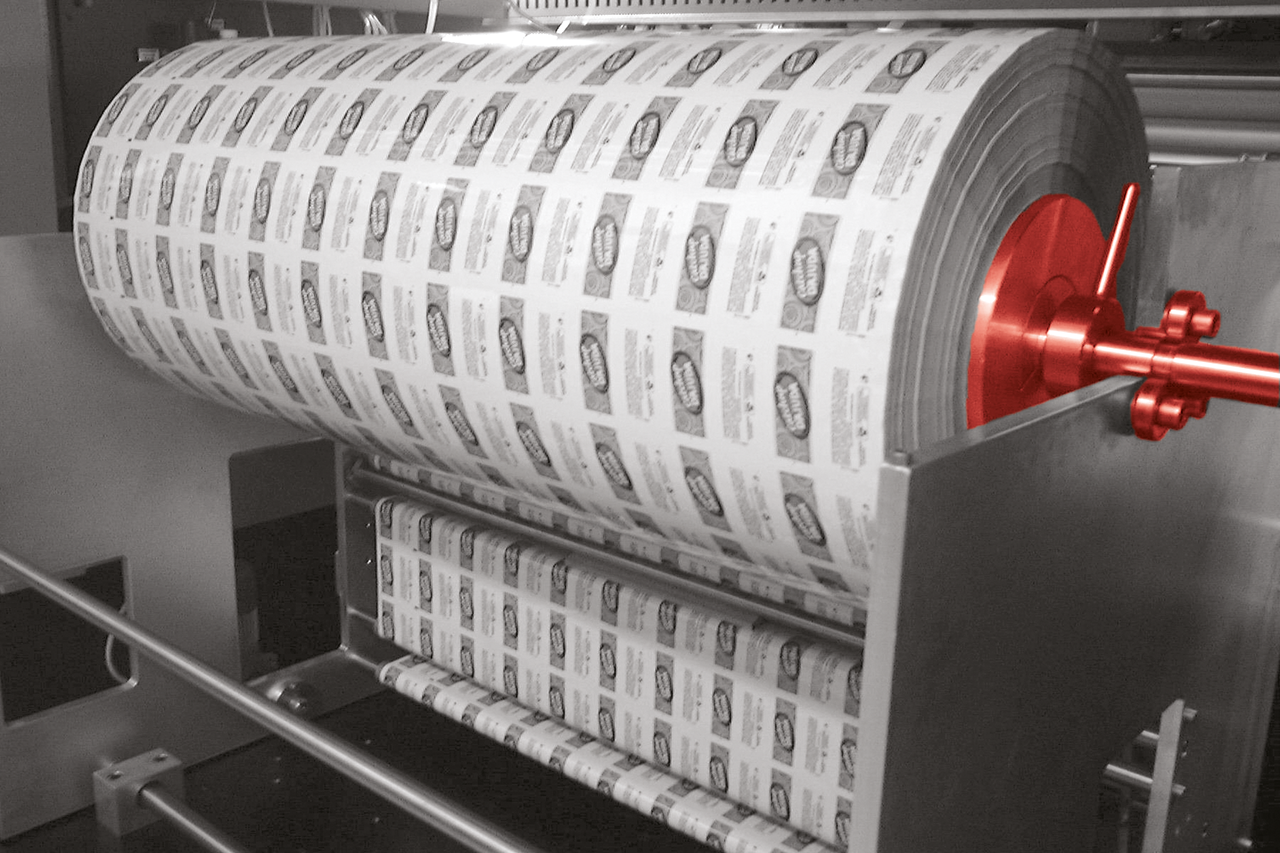
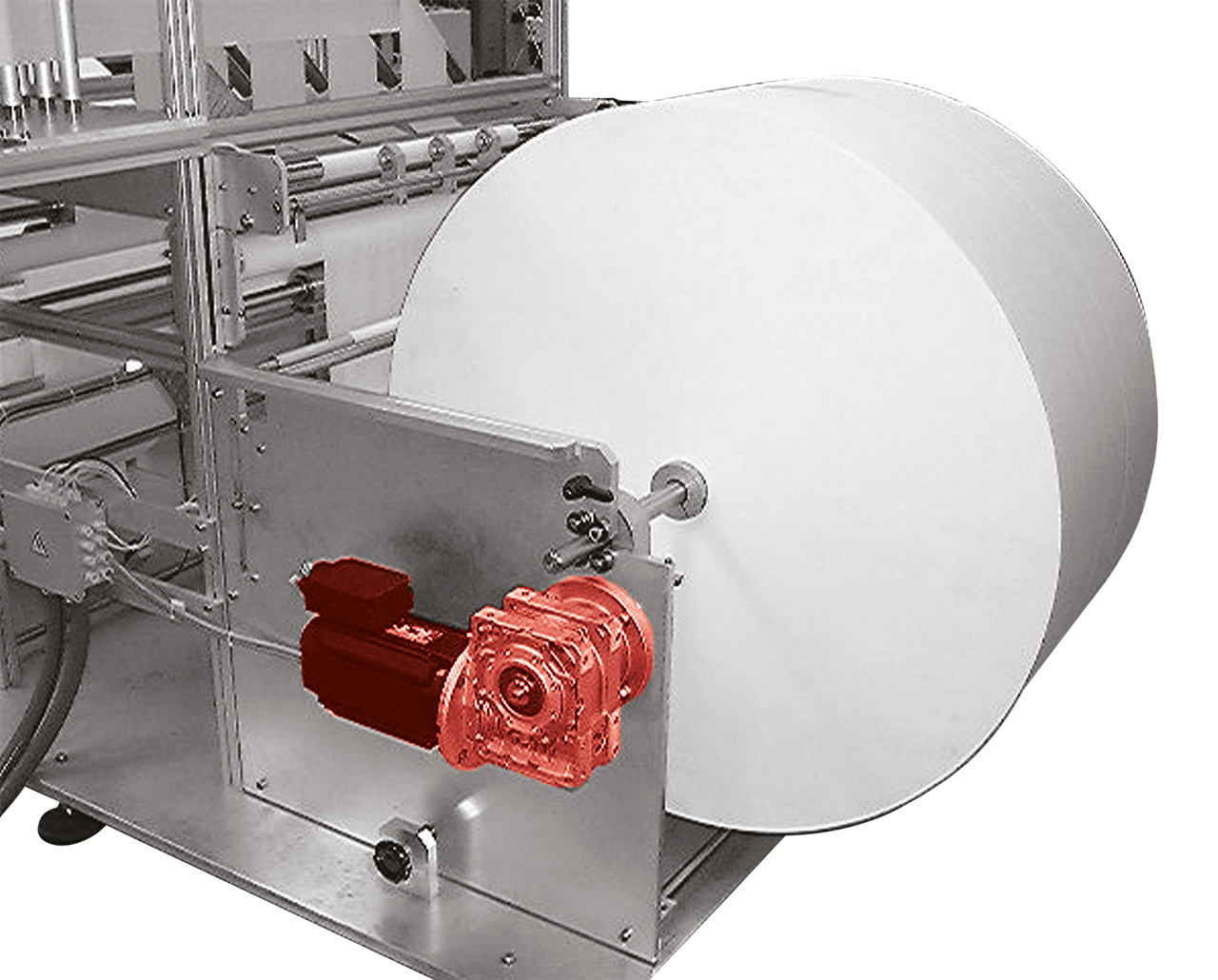
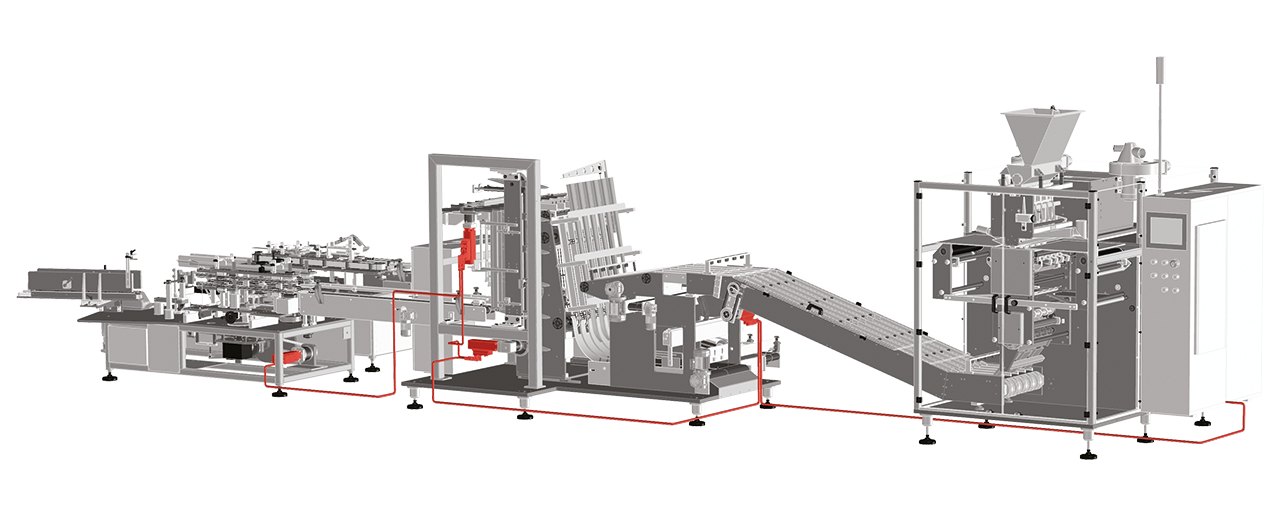