À PROPOS DE BOATO PACK
BOATO PACK fut fondée dans les années 50.
La production était à l’époque constituée majoritairement de petites ensacheuses à une ou deux pistes de production.
Dans les années 80, la société alors nommée Boato Tecsystem, devint BOATO PACK.
Au début des années 90, Boato Pack fut alors acquise par l’actuel propriétaire.
Au moment de ce rachat, le niveau technique des machines n’était qu’une évolution des modèles rudimentaires qui avaient été fabriqués dans le cours des 40 années précédentes.
La gamme de l’époque était limitée à produire avec seulement 2 ou 3 types de doseurs volumétriques, ayant une large plage de dosage et produisant à des cadences très basses.
La nouvelle gestion décida alors d’évoluer vers une nouvelle gamme d’ensacheuses en mesure de satisfaire les besoins des clients plus importants: façonniers, sociétés Multinationales et similaires.
NOTRE TECHNOLOGIE
Au-delà des différentes caractéristiques telle que la cadence, la fiabilité, la maintenance minimisée, etc., deux caractéristiques technologiques différencient nos ensacheuses des autres: flexibilité et solutions “clés en main”.
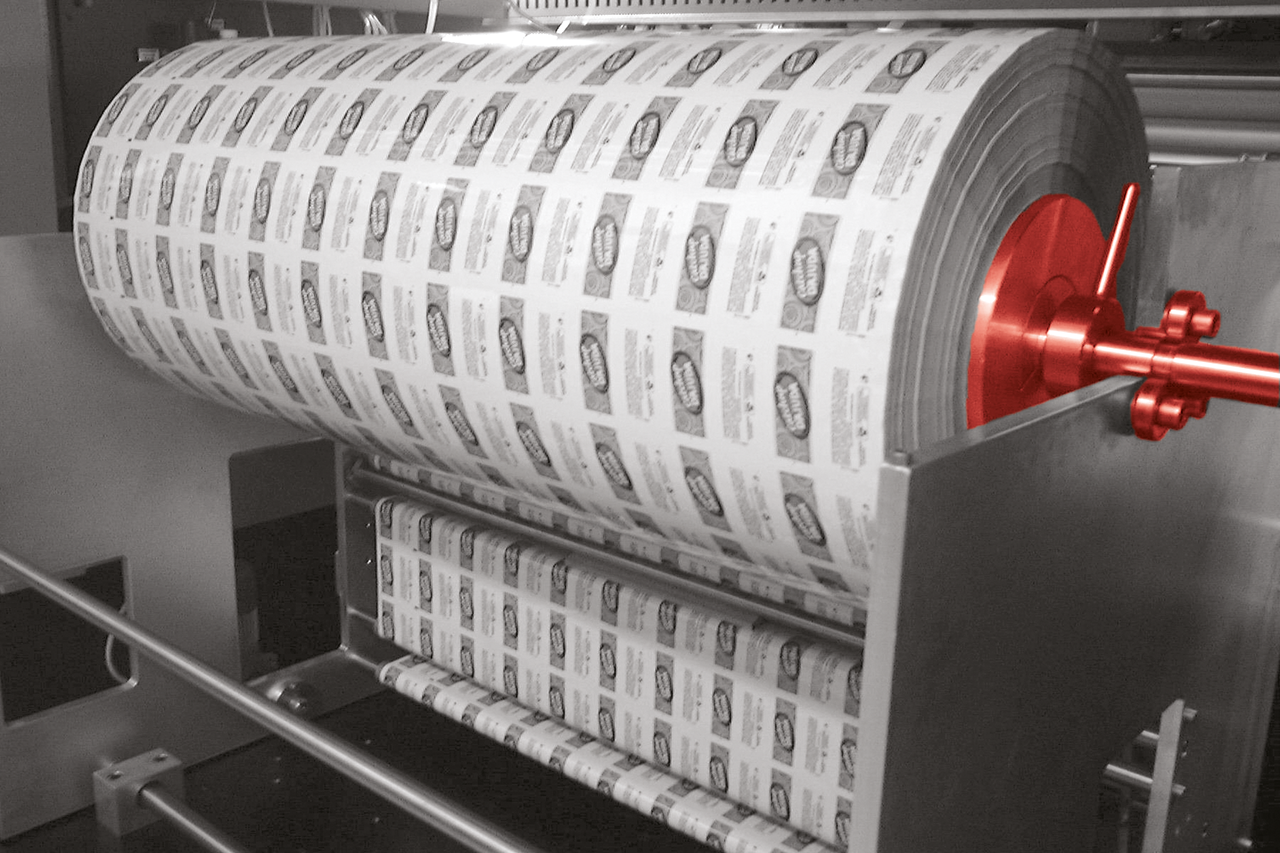
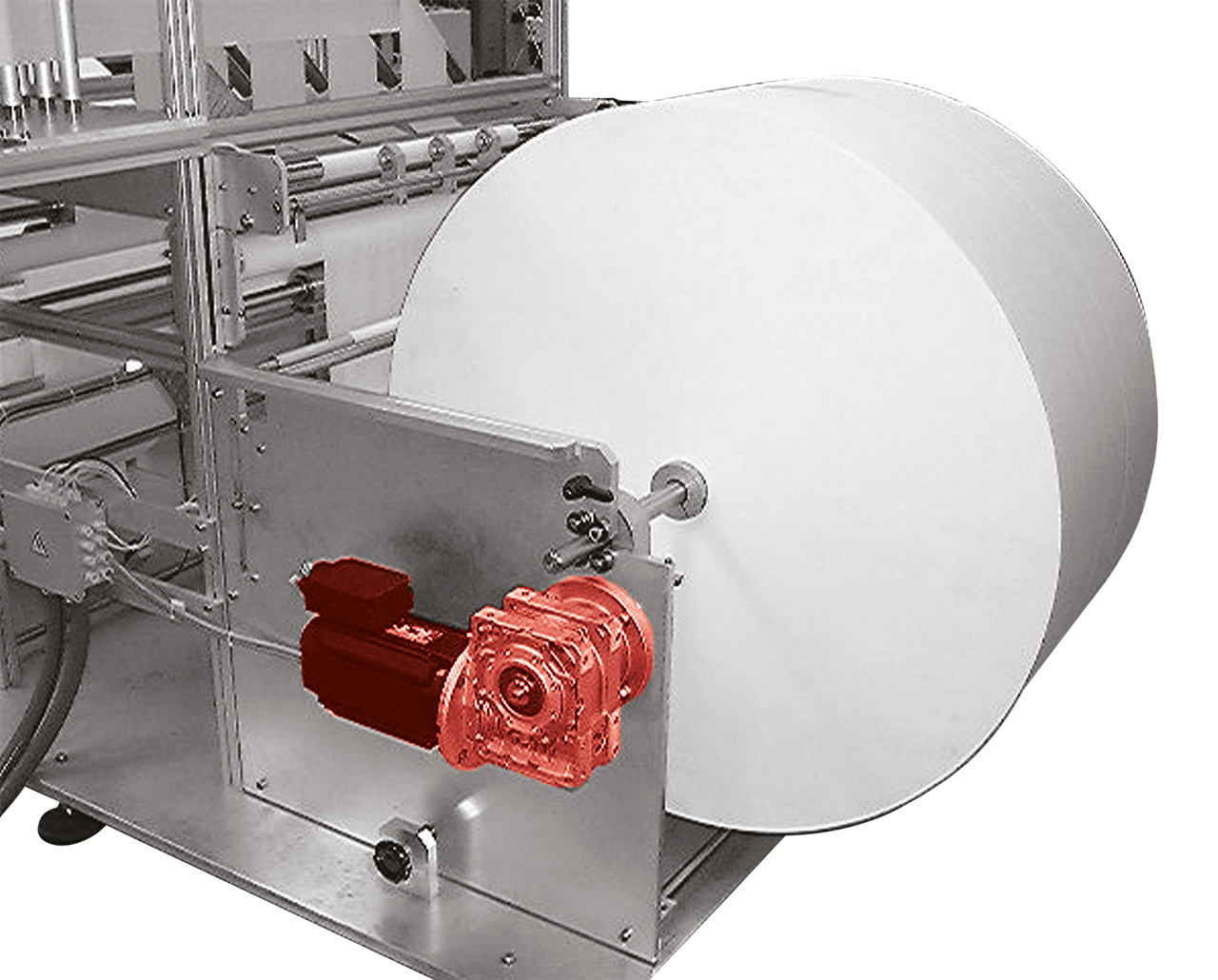
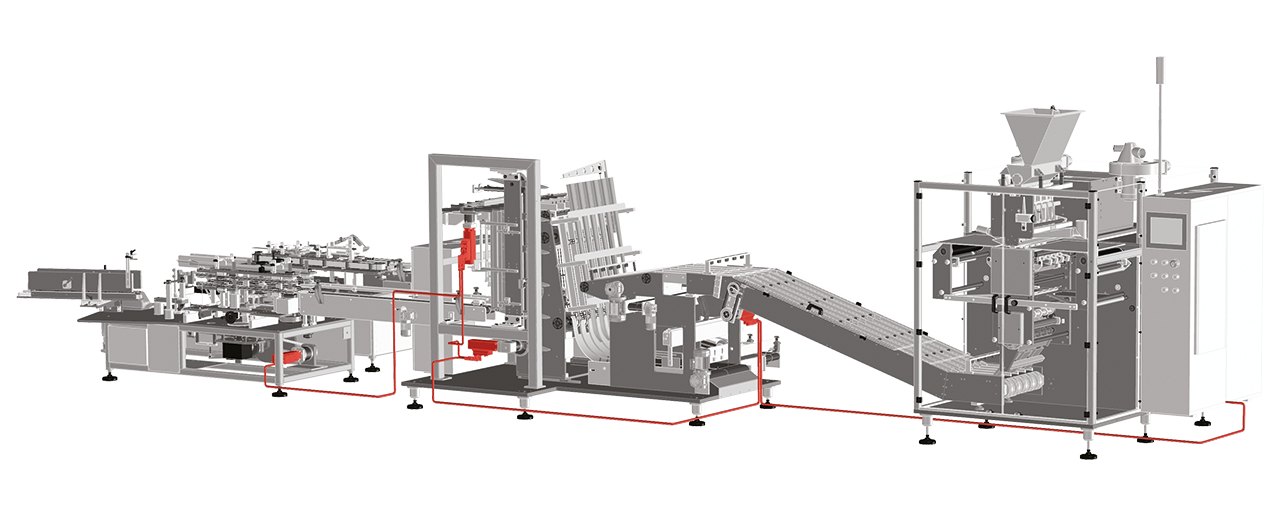